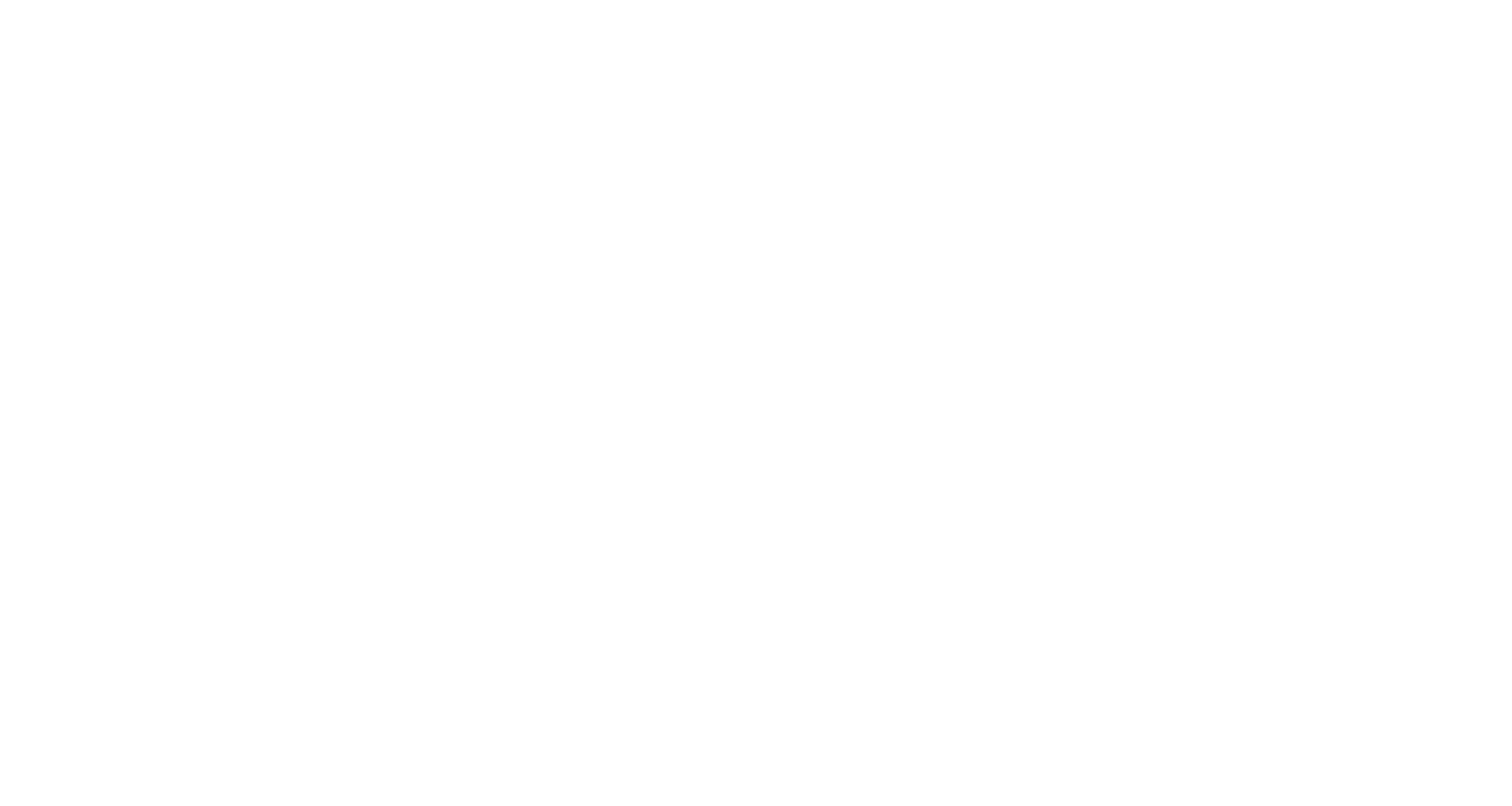
Resources
Video
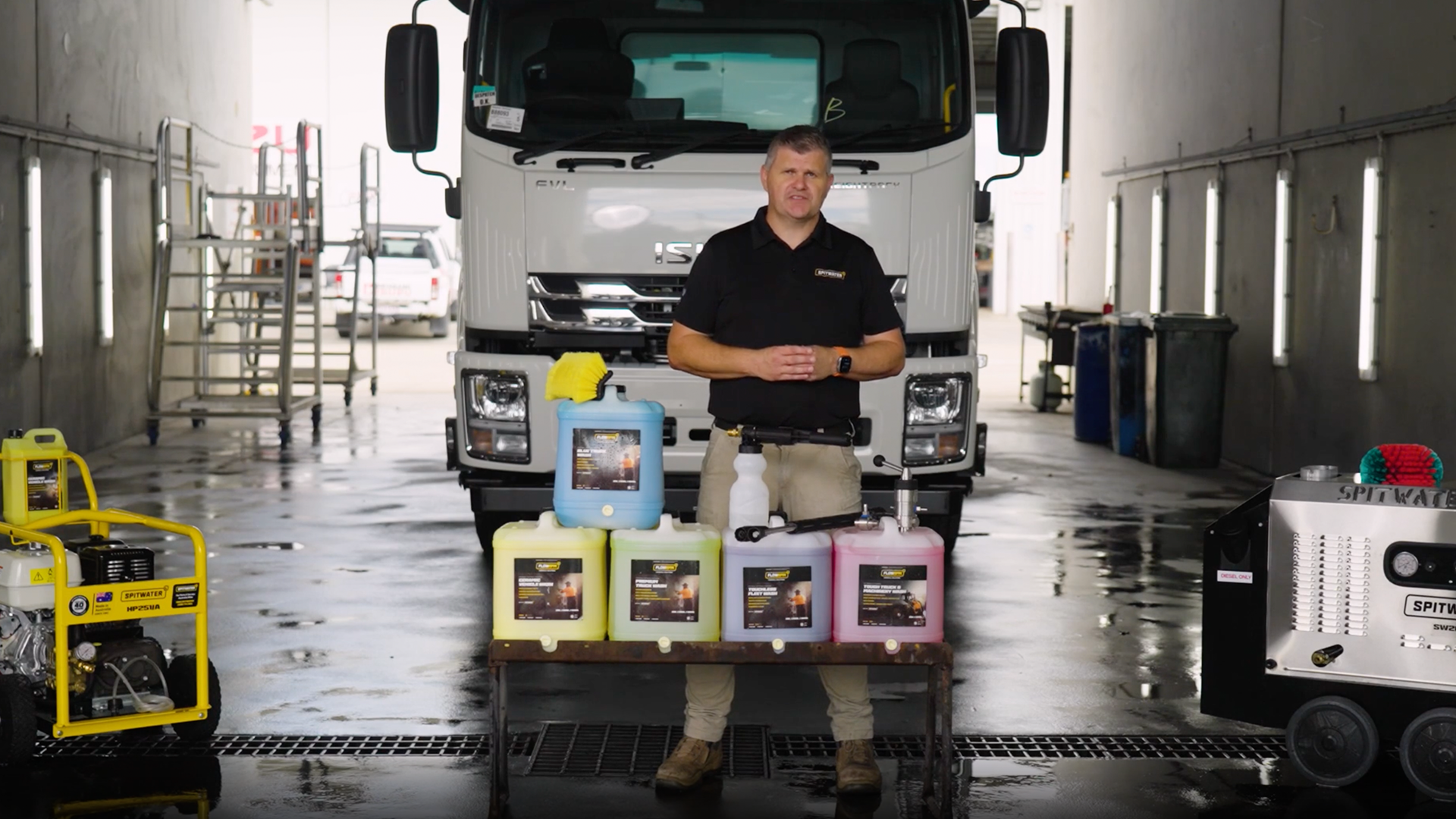
Heavy Vehicle Washing: FlowRPM Chemical Solutions Walk-through
Watch our quick video to find the right FlowRPM chemical solution for your fleet—from touchless wash to high-powered ...
Learn more
Blog
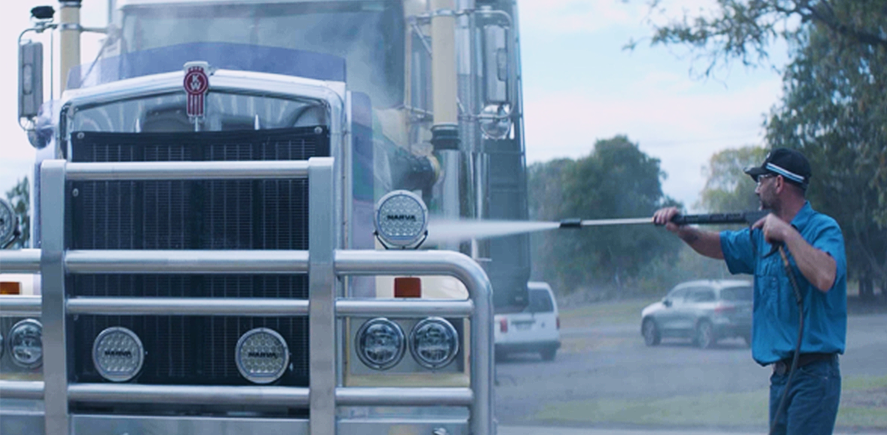
Pressure & Flow: The Secret Formula for Heavy Transport Cleaning
Discover how SPITWATER's Australian-made pressure cleaners deliver the perfect balance of flow and pressure for heavy ...
Learn more
Blog
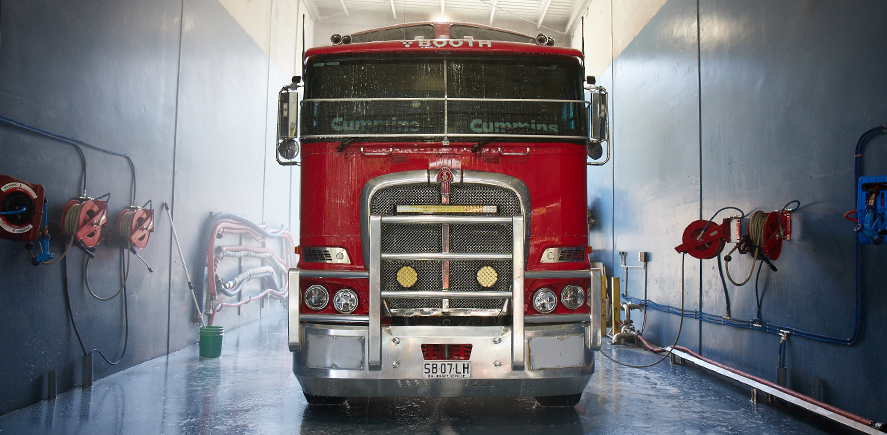
Touchless Truck Washing: The Fleet Wash Labour Saver
Touchless washing does away with the physical scrubbing of vehicles. But does ditching the brush deliver better ...
Learn more
Video
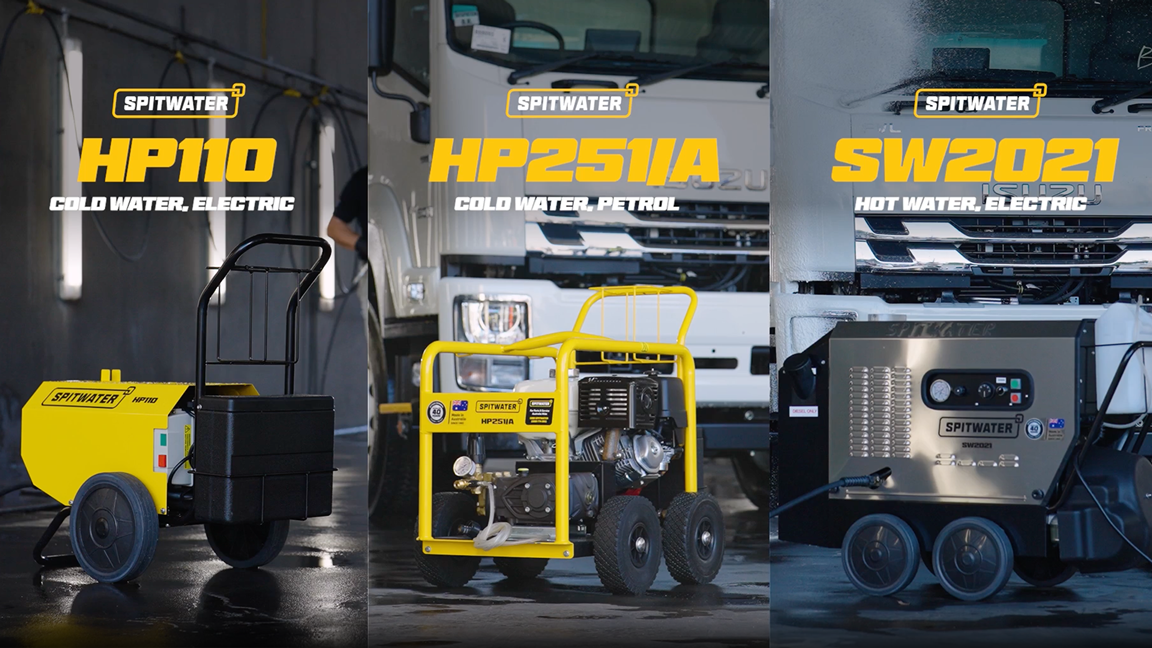
Selecting the Right Pressure Cleaner for Heavy Vehicle and Transport
In this video, we walk you through the most popular models for the heavy transport sector and share how to match the ...
Learn more
Blog
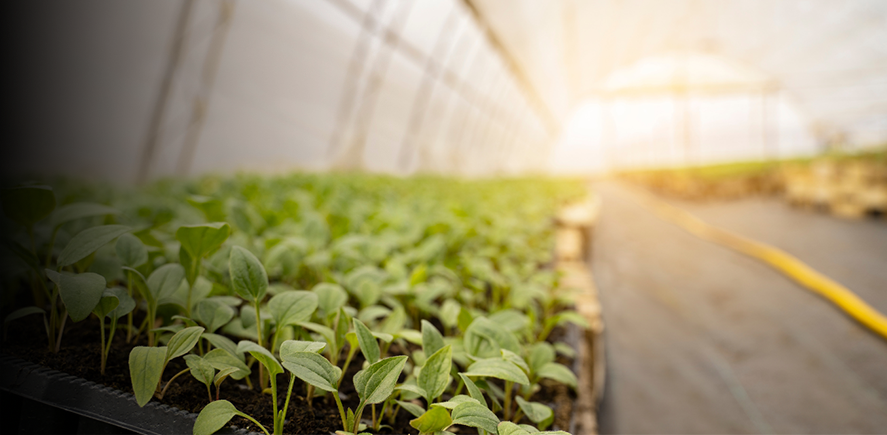
Tamborine Mountain Nursery Slashes Cleaning Time by 90% with SPITWATER
Tamborine Mountain Nursery cut bench cleaning time by 90% with SPITWATER—boosting productivity and eliminating costly ...
Learn more
Blog
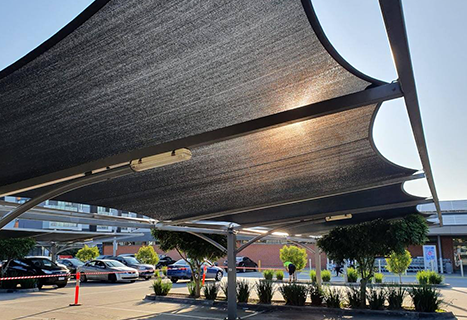
Shade Wise Keeps Shade Sails Clean and UV Effective with SPITWATER
Discover how Shade Wise uses SPITWATER to restore and maintain shade sails with ease—powerful, fabric-safe cleaning ...
Learn more
Blog
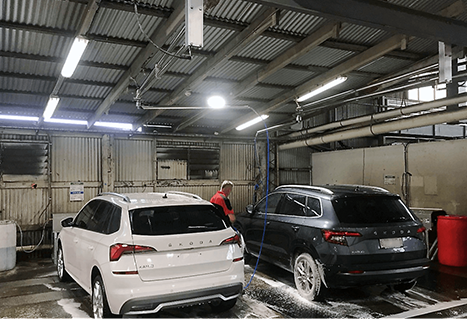
Brisbane City Automotive Halves Vehicle Wash Time with SPITWATER Custom System
Brisbane City Automotive cut vehicle wash times in half and eliminated wash bay delays with a custom SPITWATER pressure ...
Learn more
Download
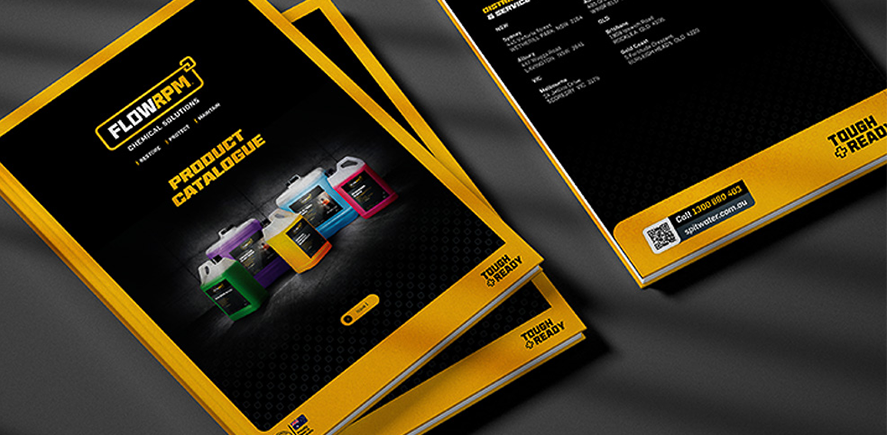
FlowRPM Product Catalogue
The FlowRPM catalogue is packed with a comprehensive range of industrial and automotive cleaning solutions, all ...
Learn more
Video
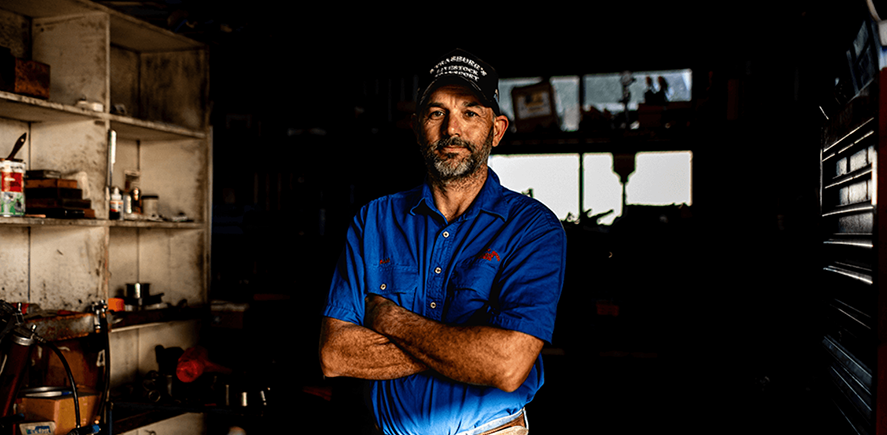
Tough Meets Tough: Strasburg Livestock Transport Relies on SPITWATER
Sam Collins of Strasburg Livestock Transport explains why SPITWATER is the only choice for keeping their trucks and ...
Learn more
Find your nearest dealer.
To locate your nearest authorised SPITWATER dealer, please visit our dealer locator page. Simply enter your location to find the closest location for sales, parts, and service support.